Why you should use aluminium for making your parts and components
Here are some good reasons to opt for aluminium for making your parts and components :
Aluminium is much lighter than steel, and has nearly-equivalent mechanical properties
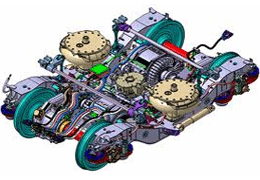
Aluminium is 3 times lighter than steel and offers nearly the same mechanical strength. For most applications the use of aluminium will therefore mean an important economy of energy because of the decrease of weight. In the German ICE high-speed train, the usage of aluminium instead of steel for the making of the bogies has resulted in a decrease of weight of 6.1 tons per wagon. Another example: a large torque-converter carter for bulldozers made of steel will weight around 600 Kg; in aluminium, it will only weigh some 200 Kg, thus increasing its MPG performance.
Feeble inertial mass
This is an important element for assemblies where certain components must accomplish repetitive linear or circular motions, with abrupt accelerations or decelerations, or direction inversions. Examples: industrial robots, punching machines or, more simply, rods and pistons for internal combustion car engines.
Good resistance to metal fatigue and dynamic strains
Resistance to metal fatigue is an important point in a wide variety of applications including automotive, aeronautical, spacecraft and railway-car construction, consumer-goods production, and so on. It should also be noted that eventual cracks in cast aluminium parts propagate very slowly; in a vast majority of cases, these cracks will be detected well on time.
Resistance to mechanical and dynamical strains: cast aluminium parts are ideal for construction elements that are subjected to compression/elongation efforts, with superposition of alternated constraints.
Aluminium has a very high ductility factor
Ductility is the ability of a mechanical part to withstand plastic deformations (and return to its original dimensions) without breaking. Cast aluminium parts do possess this property, which is important in situations where the part has to resist to abrupt constraints. Some parts of large elevators, for instance, have to withstand alternate pressure differences of up to 400 bars.
Cast aluminium has great stability of shape, and a very high deformation energy.
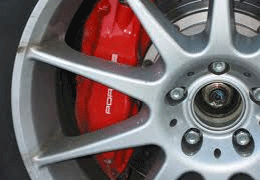
Cast aluminium parts subjected to important mechanical strains are able to deform themselves progressively without breaking, much longer than steel-made parts. This is important to avoid an abrupt breaking-off. Example: brake callipers of most cars are now made in cast aluminium. If the constraints are not exaggerated, aluminium presents an excellent stability of form.
Miscellaneous interesting points for the engineers
Here are some facts about cast aluminium parts that should be interesting for development engineers:
- Straightforward flowing-out of the lines of forces in cases of tensile, torsion or compression efforts: there are no concentrations of constraints like in welded assemblies;
- Cast aluminium parts do not become fragile at very low temperatures, as is the case with steel parts
- Assembly processes for cast aluminium parts are generally much simpler than riveted, welded, bolted or screwed assemblies. Cast aluminium parts are easily machine-tooled.
- Cast aluminium parts can easily be welded together, either with copper or even with steel parts (details available on demand)
- Cast aluminium has a very good thermal conductivity factor. Magnesium too, but it can burn in some cases.
- Cast aluminium withstands corrosion very well, even in coastal or marine environments. A protective layer of Al2O3 (alumina) forms at the surface of the part, preventing further corrosion damage.
- Aluminium is not toxic (which is important for the food industry). It is easily and economically recycled.